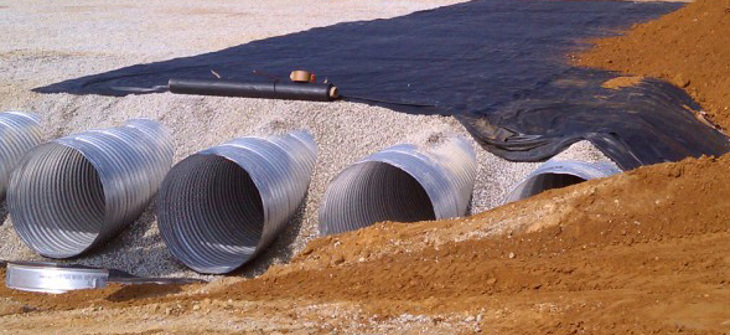
Filter Fabric in Detention and Infiltration Systems
When and How to Use Filter Fabric in Stormwater Detention and Infiltration Systems
It’s never surprising to see some type of fabric or geotextile called-out around an underground detention or infiltration system. The note is common across civil plans everywhere, but how is a geotextile selected as applicable for the particular underground system the detail was so aptly created? The answer to that question starts with one step back – why we even use filter fabric. Standard fabrics are permeable, and are designed to do exactly as their name implies. They “filter” the free-flow of water between the surrounding soil and the underground system, acting as a barrier and preventing in-situ fines and particles from entering the placed backfill. This becomes more prevalent with infiltration systems, where the design relies on the surrounding void space for storage of collected runoff.
If Civil Engineering vocabulary flashcards were created, the terms “Woven” and “Non-Woven” geotextile would be sure to make the deck. Non-woven geotextile is made of needle-punched, polypropylene fibers. “Needlepunching” is a mechanical process that interlocks the individual fibers of the soon-to-be geotextile. Once complete, the finished product resembles felt, but with much less of a rainbow color variety typically found in craft stores. The color choices are black or black. The choice in fabric weight, however, does provide a few more options. The geotextile is manufactured in lightweight, medium weight, and heavy weight, which is designated in ounces per square yard (oz/sy). Lightweight fabric is designated as a weight between 3-5 oz/sy. Medium weight is designated as 6-8 oz/sy, and heavyweight tops the scale at 10-16 oz/sy. Typically, lightweight, non-woven fabrics are specified for underground detention systems. Medium weight and heavy weight geotextiles are more applicable in erosion and stabilization applications.
Woven geotextile is less common in underground detention applications. These geotextiles are more typically used for load stabilization, roadway designs, erosion control, and landfill leachate collection systems. Similar to non-woven fabrics, woven geotextiles are also manufactured from individual polypropylene fibers. The difference is the fibers are individually woven to provide greater strength in the material, making it better suited for the applications described above. Once complete, this geotextile resembles a burlap sack.
Location and placement of geotextile can vary from project to project, depending on the Civil Engineer’s specifications. Some projects may require only the side and bottom of the excavated trench to be wrapped with fabric, where others may also incorporate the top. Regardless of the specified location of fabric, one of the biggest issues that can arise is an unaccounted waste factor. A perfect world places a roll of fabric end-on-end, neatly wrapping the trench. Reality is not so cut and defined. Real-world installation calls for overlapping of fabric as a roll dwindles and a new one is started. This overlap over an entire system accounts for “waste”. It’s also inevitable that some fabric will get damaged in the installation process, adding more to that total waste factor. When estimating the fabric quantity required for a system, a safety factor is usually added to help account for the waste that will occur in the field.
Adding a barrier around an infiltration system will help prolong its life and function, keeping the necessary backfill void spaces free and clear of fines. Solid systems will also benefit with the engineered transition between the native material and the backfill.