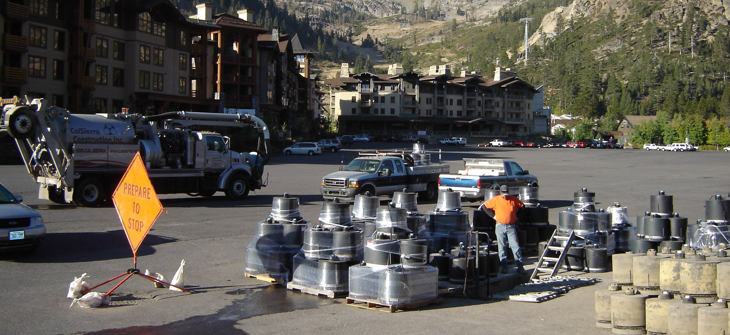
Designing Manufactured Treatment Devices with Maintenance in Mind Part 2: Access, Location, and Onsite Logistics
How Access, Location, and Logistics Impact MTD Maintenance Efficiency
In the part one of this blog series, we looked at Factors That Drive MTD Maintenance Costs. These include time and equipment, disposal costs, and consumables. Next, we explore the three factors that are most important to consider when designing MTD’s with maintenance in mind include access, location, and onsite logistics.
Access
When talking about access to the MTD, the first thing we think of is manhole covers, which are the most common choice as they are inexpensive (typically under $1,000) and easy to work with from an inspection and maintenance perspective. The most commonly used manhole cover sizes are 24” and 30”, and they are rated for heavy-duty traffic loading. Other options can provide more access to the internals of certain devices, but there is often a tradeoff between accessibility and cost.
Trench covers allow access to the entire top of the structure, but they're more expensive (typically over $1,000), can be difficult to remove, and are not the most aesthetic option. They are available in 24” width x various lengths to accommodate different MTD vault sizes, and they are typically rated for heavy-duty traffic loading. Hatches (Exhibit A) also offer excellent access, are hinged for easy opening, but are the most expensive option (typically over $2,500). A 48” x 48” hatch is frequently used on MTD’s. Hatches come in many different square and rectangular options as well as different load ratings, including pedestrian, non-heavy duty traffic, and heavy-duty traffic.
At times, a combination of covers can be used, with traditional manhole covers being used for inspection ports and a hatch located where confined space entry is needed. Most access castings can be sourced in a heavier duty load rating when required for projects such as airports or shipping terminals.
Location
Another critical factor is the physical location of the device on the site. Manhole covers, trench covers, and hatches are not visually appealing, and they may present a trip hazard. As such, placement in walkways and in front of entrances should be avoided.
Attention should also be given to the frequency of inspection and maintenance events and how they impact both pedestrian and vehicular traffic at the site. Inspection events will typically last thirty minutes, while maintenance events may take thirty minutes to several hours to complete depending on the type and size of the MTD. These events will usually take place during regular business hours. The engineer needs to assess both vehicular and pedestrian traffic flows to see how these events will impact movement.
Onsite Logistics
Closely related to location is onsite logistics. Different MTD's require various maintenance activities. An engineered bioretention system may be possible to maintain with minimal crews and equipment. In contrast, most underground systems will require a vacuum truck, support vehicles, and possibly space for the staging of consumables.
Special consideration needs to be given to those systems that will utilize a vacuum truck for maintenance. Vacuum trucks can weigh up to 25,000 lbs and should not be driven on grass or landscaped areas. Also, vacuum trucks usually charge per hour of service. Generally speaking, there is a tradeoff between a vacuum truck's efficiency and capability. The closer the MTD is to the truck, and the shallower the system, the more efficient the vacuum truck can be, and the fewer hours will be needed for the maintenance event. The deeper the system or, the farther away it is from the vacuum truck, the less efficient the vacuum truck will be, and the longer the maintenance event.