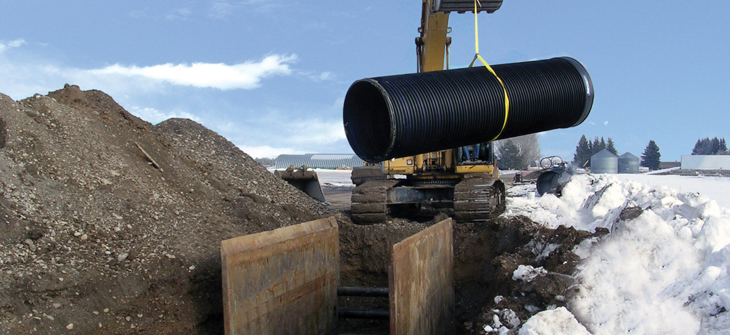
Things to Consider for Large Diameter Gravity Flow Thermoplastic Sewers | Part 2
I know you all have been waiting with baited breath to find out the in's and out's of the last two considerations when evaluating a large diameter flow thermoplastic sewer solution. To recap, typically, the larger diameters tend to have far less directional changes and lateral connections. Also, interceptors tend to have deeper heights-of-cover in gravity flow applications. Many interceptors are designed to flow 50% to 70% full, with minimal slope, deep covers, and within groundwater (requiring dewatering installation). It is also not unusual for new interceptors/trunks to be miles of pipe using several diameters.
When looking to develop thermoplastic pipe specifications, engineers might want to consider these areas of concern: hydraulics, watertightness, deep covers, and connections. Now, we’ll take a look at the last two in detail.
Deep Covers
It is not unusual to see an interceptor with 25 to 30 feet of cover. Again, considering not all thermoplastics are the same, designers should understand the importance of structural design using these materials in large diameters. Many engineers do not know that there is really only one design methodology for direct bury gravity sewer, which is within the AASHTO LRFD Design guidelines. Within the structural design calculations, weaker thermoplastics with low modulus have a unique design factor know as the Vertical Arching Factor (VAF) that allows loads to be reduced based on the theory of circumferential shorting and soil arching. For HDPE/PP, this factor could be upwards of 40% to 50%. Without this factor, the maximum covers would be drastically less. On the other hand, steel materials do not utilize VAF and therefore the design maximums are more straight forwarded with a much longer history. This is why Steel Reinforced Polyethylene (SRPE) materials are published within AASHTO under the steel design methodology and therefore does not apply a VAF. Many engineers try to compare thermoplastics based on a laboratory QA/QC value derived from a parallel plate test resulting in what is called Pipe Stiffness. This is a false equivalency comparison and should only be used to compare like materials (PVC vs PVC) for directional considerations. More importantly the use of the design guides provided by AASHTO and ultimate strength values provided by stub compression testing should be used to compare differences in thermoplastics.
Connections
Connections in this application are generally at manway access points or lift stations. There are some lateral connections, but generally these are few and far between compared to the Collection System design. It is interesting that the industry is very accustomed to think only in terms of concrete manholes or structures for these access points. Many are now seeing that large diameter thermoplastic materials can have some alternatives to this and provide for a better overall design. Many access points can be done simply by coming off the top of the mainline with a thermoplastic riser that can include ladder rungs. Also, due to the typical straight in-and-out nature of these diameters, many pipes can be simply run through a “dog-house” type of manhole base and maintain a continuous invert without cutting pipe. The pipe simply comes with a stub riser for entry or the top can be cut off in the field. Either way, eliminating leakage points and reducing hydraulic losses at the manholes is considered a benefit.