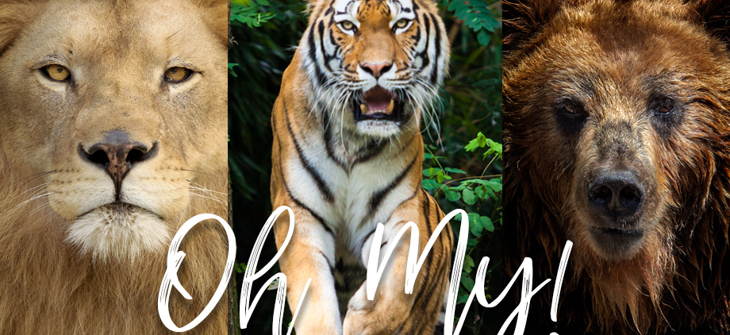
Glycol and Chemicals and Waste, Oh My!
Being in the wastewater industry, I felt an unexpected sense of pride when my 5-year-old daughter asked me about “poo” as she sat in her car seat on the way to school. I cheerfully started to explain how pipes carry waste to the treatment center, but she interrupted with “Daddy, Winnie the Pooh lives in the Hundred Acre Wood” … sigh. It’s times like that when I’m glad there are blogs to share information on topics that many family members may not be too concerned about… like wastewater pipe systems.
As a civil engineer, what goes through a particular pipe and how it affects the pipe should be of interest and concern. What are the effects of sanitary effluent on the pipe material? What about other pollutants and chemicals? What about abrasion?
One of the primary concerns in a sanitary sewer system is the formation of hydrogen sulfide gas, which is produced by the biological reduction of sulfates as organic matter decomposes. H2S gas is not only toxic to humans, but can be very corrosive to certain pipe materials, such as reinforced concrete pipe (RCP). This is especially concerning for areas of the system where effluent can be stagnant for a period of time, such as pipeline bellies, manhole structures, or pipe leading to pump stations. Therefore, the pipe material’s ability to withstand this type of corrosion is important.
In regard to storm sewer systems, the EPA has targeted certain pollutants which are prohibited from being released into storm drains and ultimately making their way into our streams, rivers, and coastal areas. Runoff with harsh contaminants should be kept out of storm drains and sent to an underground holding tank or routed to a municipal wastewater treatment facility for proper processing. A few examples of the contaminants which can find their way into storm water runoff are:
- Glycols – Typically, this is a solution of propylene glycol, water and thickening additives used at airport deicing facilities to prevent ice accumulation on the aircraft. This solution is heated and pressure-sprayed directly onto the aircraft.
- Fire Suppression Chemicals – Some foaming fire suppressants such as aqueous film forming foam (AFFF) are effective for extinguishing hazardous liquid fires, but the runoff must be contained and sent to a treatment facility. These types of systems are used primarily for aviation hangars, chemical plants, military facilities, oil refineries, and other commercial applications.
- Industrial Wastes – There are many types of wastes created from various industries including: textiles & leather, pulp & paper, ironworks, chemical refineries, microelectronics, and mining. Many of the contaminants in waste flow from these facilities must be discharged into the municipal wastewater system or a large diameter containment tank.
There are a lot of scary things going on inside gravity sanitary pipes and even more terrifying things travelling with storm water runoff in some applications, but there is an excellent pipe material to consider, which can handle all these critical applications: DuroMaxx® steel reinforced polyethylene (SRPE). Whether you’re designing a large diameter trunkline or considering a high-capacity containment tank system, DuroMaxx® SRPE technology checks all the important boxes:
- Corrosion Resistance & Durability: DuroMaxx® is manufactured using high quality HDB virgin stress-rated HDPE resins. Using resin with a Hydrostatic Design Basis (HDB) rating is a must to ensure long term strength performance characteristics of the plastic. HDPE has excellent chemical compatibility and its ability to perform successfully in these corrosive environments is well documented.
- Structural Integrity: The structural performance of DuroMaxx® comes from high strength 80ksi steel ribs which are fully encapsulated inside the plastic. Although DuroMaxx® looks like a thermoplastic pipe on the outside, the structural design methodology is very similar to corrugated steel pipe design per AASTHO Section 12 LRFD. This means there is no slow growth stress cracking or creep associated with DuroMaxx®. The ability to handle heavy live loads and high cover is achieved in diameters ranging from 30” all the way up to 120”.
- Watertight Joints: DuroMaxx® offers reinforced Bell & Spigot joints (30” – 72”) as well as fully welded joints (36” – 120”). These joint types have been tested to meet or exceed ASTM D3212 standards for water tightness.
- Abrasion: The abrasion resistance of HDPE has been scientifically tested multiple times over the years to outperform other pipe materials, including concrete and fiberglass. The excellent ability of HDPE to withstand wear and abrasion, even in harsh acidic environments, is well documented.
- Value: From a material price standpoint, DuroMaxx® can be very competitive with concrete and fiberglass pipe materials – especially in larger diameters. The ability to provide long lay lengths (40’ long sections can be supplied in all diameters) means faster installation and fewer joints for the completed system. Inline fittings (access risers, stubs, manifolds, elbows, etc.) are another benefit of the DuroMaxx® technology.
With all of that said, I’m glad our industry has a technology like DuroMaxx® available, so the only “poo” my daughter has to concern herself with is Winnie the Pooh.