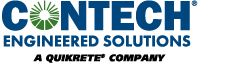
Culvert replacements are a common reality for all owners of drainage infrastructure and a routine part of maintenance and expansion projects on federal lands, roadways and railroads; state department of transportation (DOT) roadways; and at the local level with county, township and municipality owned transportation corridors. Fortunately, culvert rehabilitation via relining has gained momentum as a viable alternative to culvert replacement when dealing with aging drainage infrastructure. Whether an owner of a culvert wants to take a traditional design and delivery approach or conduct the work themselves, the construction methods of many reline options can be performed by parties whose normal work activities don’t include reline construction. In addition, most methods can be performed by in-house maintenance teams or entities who do more traditional open cut drainage work.
The decision-making processes leading up to reline construction activities can be a bit more involved than for conventional replacement, and the making of uninformed reline decisions can lead to major installation challenges or unexpected final results. This course will attempt to categorize the process of designing a culvert reline project, hoping the reader becomes more informed and feels more confident about tackling the design and implementation of a culvert reline project.
Step 1: Assessment of the Existing Culvert
Various resources exist that cover all areas of pipe inspection, including documents from the pipe industry and the Federal Highway Administration (FHWA) (see the References at the end of this course for more information). Some state DOTs have written their own procedural guidelines on relining.
The first step is to assess and evaluate the existing culvert, but not just its current condition. An attempt to find installation records and original plans can be important in understanding the material types involved and how it may have been installed. Culvert materials have very different characteristics when it relates to remaining service life, original vs. existing geometric shape, hydraulic capacity and remaining structural capability. A proper culvert inspection includes getting an interior look (via man-entry or entry with video/photographic equipment). It also includes an accurate assessment of what’s observed. A good assessment will include answers to the following questions:
1. How old is the culvert, and what has it been exposed to from a wear and tear standpoint?
2. What is the culvert material type, and how was it installed and backfilled?
3. What is the physical condition of the culvert?
4. Are there areas of concern that may cause this pipe to deflect, move, become disjointed or collapse before a reline project can be initiated?
5. Could proposed work activity initiate any of
the above?
6. How much time is available to get the work designed and completed?
7. Is there adequate room for safe access, cleaning and reline work to occur?
8. Which geometry variations could pose challenges to any potential reline processes?
It’s important to note that it’s risky to only look at culverts of any size from the inlet and outlet end to draw conclusions about alignment and grade variations. If a culvert is large enough to enter, entering and taking a close look at the condition (in a safe manner) is paramount to understanding the culvert.
A longitudinal sag can look like a pure deflection at the middle of the culvert, whereas close measurement could reveal there is no deflection, only a significant sag due to overall settlement under the higher embankment. Taking 2D/3D shape measurements is essential, but tying them into elevations will make the information much more valuable.
Knowing the issues and damage is critical from a structural standpoint, but damage that may be cosmetic also is important. Relying on knowledgeable parties who are experts with regard to specific types of pipe is important. Industry professionals can be valuable resources.
Generally, the assessment phase collects critical information used in the hydraulic design such as hydraulic input parameters and knowing what can fit. Field information also contributes to the structural design (knowing the live and dead loads that must be carried) and construction planning (how much room is available and what access is available).
Step 2: Hydraulic Analysis
Jurisdictional design criteria and methods for hydraulic design of a specific culvert must be followed, but the following information may be helpful. Hydraulic analysis of the existing culvert (assuming it has been cleaned out) can provide a flow capacity for the existing condition as well as a presumed design headwater depth limitation. This requires a design flow and some important information about the situation (e.g., tailwater depth, slope, host pipe size, Manning’s ‘n’ of the host, etc.).
Culverts often operate hydraulically in Inlet Control, meaning the flow capacity is directly related to the waterway area and inlet conditions. In Inlet Control, pipe roughness, slope and length aren’t critical, but those properties must be known to properly evaluate the overall hydraulics. A qualified engineer should be engaged to do this comparison between original and relined condition.
A simple full-flow comparison using Manning’s formula is not the whole story. If a culvert operates in Outlet Control, then a smooth reline product may be quite favorable. However, additional hydraulic performance challenges may be created by a reline culvert (much faster outlet velocities, for example). The FHWA maintains a free hydraulic analysis program appropriate for culverts available for download at https://www.fhwa.dot.gov/engineering/hydraulics/software/hy8/.
Although the supporting documentation is extensive, it requires knowledge and training in the fields of hydrology and hydraulics, so engaging a qualified Professional Engineer to run the hydraulics (and determine the necessary input information) is always a wise investment.
Don’t forget how significant the inlet configuration can be on hydraulic performance. Lowering the inlet loss coefficient through improved end treatments often can overcome reductions in waterway area, but a qualified person needs to make these types of analyses.
Step 3: Selecting a Rehab Option or Reline Material
Based on the assessment of the existing culvert as described in Step 1, it may be determined that only rehab of specific aspects of the existing culvert are required. Rehab options can include the use of a reinforced concrete paved invert. The California DOT developed a viable method that requires the original wall thrust carried by a host pipe to be transferred to and carried by the paved invert. Its Design Information Bulletin on the topic walks through this process.
Isolated and targeted joint repairs, spot repairs, coating repairs, etc., are viable rehab methods when the assessment warrants such an approach.
In rehab or reline cases in which the desired hydraulic capacity can’t be reached, viable options include the construction of an additional culvert using trenchless methods or tunneling around the outside of the original pipe to create a larger culvert.
Cured in place pipe (CIPP) is a common and effective relining approach for smaller-diameter smooth-walled pipes. It’s also a viable option for corrugated metal pipes in areas where freeze/thaw isn’t severe (due to the entrapment of water in the gaps between the CIPP lining and the host pipe’s corrugations).
Centrifugally cast concrete linings have been in use for relining since the 1930s and are available in cement-based and geo-polymer versions.
Segmental sliplining remains the most-popular relining method, likely because of the low cost and high confidence in the well-established structural design methods associated with them. Material service life design is well established, including newer corrugated metal options that can provide 100 years of maintenance-free service in the recommended environments.
Relining or using a partial tunneling method is an option where deflections or other distortions exist that would normally prevent segmental sliplining. One approach is to open up the restrictive areas with tunneling methods to provide room for sliplining. Another approach is to use tunnel liner plate to build the new pipe “as you go,” and use a material that’s well suited for the desired service life of the new culvert. Hot dip galvanized steel, aluminized steel type 2, polymer pre-coated steel and aluminum tunnel liner plate are available in a variety of shapes that can help solve tough reline challenges.
A note on pipe arches: the original geometric dimensions, especially the radius and location of the haunches (also referred to as “corners”) of corrugated metal pipe arches can vary significantly from size to size, even in comparison to industry tables from historical design documents. It’s important to get a good set of measurements on pipe arches and look for uniformity of those measurements along the length of the culvert (and tie them into fixed survey points to check for sag and curves). A new segmental pipe arch may not be a good fit, even if comparing the span and rise looks favorable. A detailed survey can help avoid a fit-up surprise during construction.
No matter the method selected, close interdependence on the field assessment information gained in Step 1 and the hydraulic information gained in Step 2 must be maintained.
Many materials can be considered for segmental sliplining, including the following:
Round Shapes
• Corrugated PVC Plastic Liner Pipe
• Solid Wall HDPE Pipe
• Steel Reinforced Polyethylene Pipe (SRPE)
• Machine Wound-in-place SRPE Pipe
• Profile Wall HDPE and Polypropylene Pipe
• Fiberglass Pipe
Round and Pipe Arch Shapes
• Ovalized Solid Wall HDPE, Aluminized Type 2 and Polymer Pre-Coated Corrugated Metal Pipe
• Steel and Aluminum Spiral Rib Metal Pipe
• Polymer Pre-Coated Steel Double Wall Pipe
Round, Pipe Arch, Ellipse, Arch and Box Shapes
• Steel and Aluminum Tunnel Liner Plate
• Steel and Aluminum Structural Plate (aluminum bolts are available on ALSP)
Others
• Precast Concrete Arches
• Smooth welded, CIPP, spray on linings, etc.
Step 4: Structural Design
Although the term “reline” indicates a material is simply a liner and not necessarily a new structural load carrying pipe, a fully structural load carrying reline pipe typically is needed. If a culvert is lined early enough (rarely the case), a reline pipe can be designed as a hydraulic or service-life enhancement, and it may not have to carry the original loads of the host pipe. This approach assumes the host pipe will continue to perform as originally designed for the desired service life, and it won’t corrode, break down, deflect, become dislodged at the joints or undergo any level of future degradation.
There may be situations where a reduced load approach can be taken. Otherwise, a reline pipe must carry all loads that the host pipe was designed to carry. Actual active loads acting upon a reline product or pipe within an existing pipe can vary significantly depending on the following: existing pipe material, timing of the project relative to backfill or embankment saturation, type of fill material and its physical properties, type and cross section of the original bedding and structural backfill envelope, nature of the original construction methods, degree of deterioration of the host pipe, live loads, and depth of cover, among others. The nature of groundwater and surface water movements through the fill also can have an impact.
To consider use of a reduced load approach, the following areas should be evaluated:
• Installation technique of the host pipe
• Design method of the host pipe
• Detailed soil data for the soil backfill zone in its current state
• Detailed soil data for the current trench or embankment fill zone in its current state
• Detailed condition assessment of the host structure to make sure there are no signs of a compromised backfill zone, no deflection beyond the original deflection, and no potential for further deterioration of the host after the reline process occurs
• Original cross sections and topographic information to gage potential for groundwater movement
• For shallow installations, design for appropriate live loads per current industry standards
• For shallow installations and where the host pipe backfill zone properties aren’t known, design for stiffness and bending strength as if it were new construction
Due to the complexity of trying to define the aforementioned variables, many agencies and engineers have prudently decided to assume the new pipe needs to carry the same loads as if the installation were conventional direct burial.
Step 5: Constructability Review
This phase of the design process ensures the selected material option can be built at a reasonable cost; the best way to do this is to perform a detailed reline procedure analysis. Creating a step-by-step sequence of events and determining the manpower and equipment needed as well as the amount of time each major task requires will help tie down a budgetary cost. Of course, the surest way to determine hard costs is to detail the project and bid it out. Local contractor availability is critical to the actual cost. If work is done internally, consider hard capital costs as well as soft labor costs (i.e., opportunity costs, meaning “what work won’t get done if we reassign certain workers to this reline effort?”).
Step 6: Develop Plans and Specifications
If a project is being bid in a traditional “design-bid-build” approach, the better and more extensive the plans and specifications, the more likely superior quality and increasingly competitive bids will be received. It’s important not to “over detail” some reline-related items that will require flexibility during construction, which may stifle creative thinking and problem solving by a contractor.
The following list of contractor submittal requirements also enables for some creativity on means and methods, but allows the owner or consulting engineer to review the contractor’s thinking:
Reline Installation Submittal Requirements
1. Detailed installation plan
2. Material certification
3. Structural design using AASHTO LFD or LRFD methods, sealed by a Professional Engineer licensed in the state of the project
4. Detailed grouting plan, including: buoyant force calculations, lift heights, lift volumes, grout mix design, grout strengths, grout fluid unit density, initial set time of the grout, pumping pressure, grout port locations and air vent locations, as well as the bulkhead designs
5. Certification by the liner manufacturer that the grouting plan is satisfactory and complies with all precautions and limitations of the liner manufacturer
If a project is being built with inhouse crews, communication of critical design features and their importance is key.
The decision-making processes leading up to culvert reline construction activities can be complex, but this course provides a straightforward (albeit generalized) procedure for tackling a reline project. Skipping any of these steps, or not starting with Step 1, can result in challenging risks and perhaps a final product that doesn’t meet the intended results.
Hugh B. Mickel, P.E., is the Director of Reline Technologies and has 32 years of experience working for the nation’s largest producer of corrugated metal pipe products: Contech Engineered Solutions LLC. He holds a B.S. in Civil Engineering from Purdue University and has been a registered Professional Engineer since 1990.
Mitchell T. Hardert, P.E., is the Chief Engineer at CBC Engineers and Associates. He holds a B.S. in Civil Engineering from the University of Dayton and is a registered Professional Engineer in most U.S. states and Canadian provinces.
ASCE/WPCF Joint Committee (1969) – Design and Construction of Sanitary and Storm Sewers
National Corrugated Steel Pipe Association (2008) – Corrugated Steel Pipe Design Manual
California DOT “Design Information Bulletin No. 83-04” (2014)
FHWA’s “Culvert Repair Practices Manual Volume I” (1994)
FHWA’s “Culvert Repair Practices Manual Volume II” (1995)
Online quiz for this article is not active and
PDH credit is no longer available.
This article is being maintained for informational purposes only.