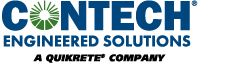
Infiltration systems are a cornerstone of modern stormwater management—but are we designing them to last? As their use expands, especially underground, new research raises concerns about sediment buildup, maintenance challenges, and long-term performance. This article takes a closer look at whether our current practices are protecting infiltration capacity—or quietly eroding it.
Learn MoreStormwater parks are an innovative solution for managing urban runoff while providing recreational and ecological benefits to communities. However, in dense urban areas, the large amount of land traditionally required for these parks poses a major challenge due to high costs, limited space, and competing land uses. This blog explores how high-rate bioretention systems offer a compact, efficient alternative that enables the development of successful stormwater parks even in space-constrained environments, with real-world examples from Washington State.
Learn MoreWith urban expansion outpacing natural infrastructure, cities face a growing challenge: managing the surge of stormwater that leads to flooding, pollution, and environmental harm. One innovative solution is the stormwater park—a green space designed not only for recreational use but also to manage stormwater through advanced engineering techniques.
Learn MoreBeing buried under dirt might be one of the most common fears people have. However, if you were a stormwater management device (or the human designing it) you might begin to worry about not having enough dirt over your system. How much is enough earth cover? Can I put too much? What backfill materials are suitable? Whether you are designing a hydrodynamic separator, a filter, or any of the diverse options of detention and retention systems; You need to know the answers to these questions, and we are here to help.
Learn MoreCivil engineers understand the delicate balance between form and function. High-rate bioretention systems, known for their efficiency in managing stormwater, offer an often overlooked benefit: aesthetics. Integrating visually appealing bioretention systems into urban landscapes can enhance community engagement, foster sustainability, and improve the overall perception of civil infrastructure.
Learn MoreWhen it comes to stormwater management and culvert design, selecting the right pipe material is crucial for performance, longevity, and cost-effectiveness. Enter Aluminized Type 2 (ALT2) pipe—a material that has become a staple in civil engineering projects. But what makes it so special? This blog will cover everything you need to know about ALT2 pipe and why it’s often the top choice for stormwater and drainage systems.
Learn MoreHydrodynamic Separators (HDS) have been a staple in stormwater management for over twenty years. Choosing the right HDS unit for your project can be challenging, but understanding key design considerations can help guide you through the process. This blog post reviews several important factors to consider when sizing your HDS unit.
Learn MoreHydrodynamic separators (HDS) are increasingly recognized as essential components in modern stormwater management systems. These devices effectively remove pollutants from stormwater runoff, helping to protect water quality and meet regulatory requirements. However, the successful implementation of HDS requires careful consideration of various design factors. This article outlines best practices for engineers to ensure the effective performance and longevity of hydrodynamic separators.
Learn MoreIn stormwater management, manufactured treatment devices (MTDs) are often recognized as innovative solutions for controlling runoff and enhancing water quality. Yet, despite their growing adoption, several misconceptions about these devices persist, leading to confusion and misinformed decisions. This blog will tackle some of the most prevalent myths surrounding MTDs, shedding light on their true capabilities and effectiveness.
Learn MoreGiven the pivotal role civil engineers play in designing and implementing infrastructure, a deep understanding of Total Maximum Daily Loads (TMDLs) ensures compliance with regulatory requirements and contributes to the broader goals of environmental stewardship and public health. This post provides detailed insights into the triggers, development, and implementation of TMDLs, emphasizing the integral role civil engineers have in achieving and maintaining water quality standards.
Learn MoreSUBSCRIBE
The Stormwater Blog is featured on the Contech Site Solutions Newsletter. Get insights, news, tip & tricks delivered directly to your inbox.