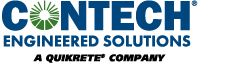
Buried flexible sewer pipes come in a variety of materials. The most common in the United States are corrugated metal (CMP), polyvinyl chloride (PVC), centrifugally cast glass-fiber-reinforced polymer mortar (CCFRPM or fiberglass), solid wall polyethylene (PE), steel reinforced polyethylene (SRPE), corrugated PE and polypropylene (PP) pipe. Design engineers often seek simple ways to compare between all of these different materials. It is easy to categorize the various materials by use of simple acronyms such as CMP, HDPE, PVC, etc.
For hydraulics, the Manning’s (n) value is utilized. For joint tightness, referencing the requirements of ASTM D3212’s 10.8 psi water tightness is the most common. In pressure applications, there are pressure ratings. It is more difficult, however, to find a simplistic way to quantitatively compare structural performance or pipe strength. One of the most common ways to attempt to compare structural performance is the use of pipe stiffness.
Pipes Stiffness per ASTM D2412
Pipe stiffness might be one of the most commonly specified parameters, but it may also be the least understood in the pipe industry. Pipe stiffness does describe a type of structural performance, but it does not accurately predict the structural results for buried flexible pipe.
Let us first understand where pipe stiffness comes from. The term itself is a value derived from the manufacturing quality test ASTM D2412 “Standard Testing Method for Determination of External Loading Characteristics of Plastic Pipe by Parallel-Plate Loading.” The test measures the load required to deflect an unsupported pipe sample, of a specific length, a distance equal to 5% of its diameter at a specific temperature and rate of deflection.
What Pipe Stiffness Is Not
It is critical to understand that the sample is not side supported by a soil backfill and therefore does not mimic actual buried flexible pipe in ring compression. The pipe stiffness value can compare a pipe’s ability to resist handling and some installation forces but has very little impact on pipe performance after the pipe is installed. Furthermore, it also can be noted that comparing pipe stiffness values for just handling and installation can be misleading and a false equivalence, since the test has very specific parameters that, when changed, result in many differences between the various pipe materials.
Note that this test came from the 1960s, and it was initially intended to ensure various qualities associated with solid wall PVC sewer pipes (e.g., SDR35) conforming to ASTM D3034 “Standard Specification for Type PSM Poly (Vinyl Chloride) (PVC) Sewer Pipe and Fittings.” Since the mid-1960s, many other types of thermoplastic pipe materials are being manufactured, and the test has been used as a similar quality assurance. Unfortunately, during the last 55 years, many engineers have misrepresented or overstated the importance of this performance value, derived from a simple “flattening” test.
46 psi or pii
The value for pipe stiffness is described in units of pounds per inch of pipe length per inch of deflection from round, or pii (lbs/in/in). Many have mislabeled this unit as psi. Others simply state PS for pipe stiffness followed by a value.
The most commonly referenced pipe stiffness is 46 pii. Where did it come from? Since solid-wall ASTM D3034 PVC pipe (e.g., Standard Dimension Ratio, or SDR) is produced with multiple thicknesses, several minimum pipe stiffness values are associated with SDR PVC pipe (SDR = outside diameter ÷ wall thickness). The most common SDR across the United States for gravity sewerage applications is SDR35. The minimum pipe stiffness for SDR35, per its specification, is 46 pii. Many agencies have used 46 pii—due to SDR35’s popularity—as the bar from which to compare all other pipe materials for sewer usage. Again, this can lead to false equivalence.
Stiffness Temperature Comparison Chart
False Equivalence—Changing Test Parameters
There are many reasons why we should not compare different materials (e.g., PVC vs. HDPE vs. steel vs. polypropylene) against one value derived from one material type such as the case in using SDR35 PVC’s 46 pii pipe stiffness. First, changing the testing parameters produces drastically different results when comparing pipe materials. ASTM D2412 uses a specific sample length and performs the test with a loading rate of ½-inch per minute and at an atmospheric temperature of 73° Fahrenheit. If in 1965 they chose different parameters other than these, then something other than 46 pii would have been considered the bar to meet. Some of the parameter change effects are as follows:
• Temperature: Some thermoplastics can have up to 50% reduction in stiffness at elevated atmospheric temperatures. This can be realized in in-situ examples when periods of solar absorption occur on hot summer days.
• Soil Interaction: The test utilizes two smooth plates. Soil interaction in an actual installation will increase the load carrying capacity of some pipe types, and this increase will vary based on the pipe’s mechanical and physical section properties. Simply increasing the friction of the plates themselves can increase stiffness results.
• Strain Rates: The test applies a load or strain at ½-inch per minute. Non-reinforced plastics and visco-elastic materials would have significant reduction in pipe stiffness at slower loading rates.
• Pipe Configuration: ASTM D2412 has a specific sample length requirement. Pipe types that are helically wrapped have increased pipe stiffness results when longer sample lengths are tested. This is not similar with annular corrugated pipe types.
Better Source to Determine Ultimate Strength?
Structurally, the parallel plate test does not subject the pipe sample to ring compression, which determines a flexible pipe’s wall thrust capacity.
The wall thrust capacity is used to determine ultimate loading or strength capabilities per American Association of State Highway Transportation Officials (AASHTO) structural design methodology. AASHTO’s pipe design methodology is the nation’s primary design method, and it does not use the value of pipe stiffness for ultimate loading resistance and performance. The design methodology does use parameters such as the modulus of elasticity and tensile strength along with values derived from stub compression testing per AASHTO T341, but not pipe stiffness for ultimate load capacity.
False Equivalence—Modulus Strength Example
Why can materials with similar pipe stiffness have drastically different performance outcomes? Answer: Mainly due to the following material properties along with the pipe profile design and orientation.
One of key material properties is the modulus of elasticity. Notice how large a difference there is between those that are visco-elastic thermoplastics and those that are not, including the creep indication from initial to long-term values. AASHTO design methodology recognizes these characteristics and also allows for a vertical arching factor (VAF) to be applied to loads associated with low modulus materials (e.g., HDPE and polypropylene). The VAFs ultimately reduce loads by up to 50% due to circumferential shortening of the weaker material types. When shortening occurs, it often can create the propagation of thin inner wall buckling perpendicular to the flow line. These inner wall waves drastically increase the Manning’s (n) roughness coefficient in sewer designs, although the material may have had a similar pipe stiffness as a 46 pii PVC material.
False Equivalence—Installed Deflection Example
A field test performed by the Utah DOT and Utah State University in July 2010 compared corrugated HDPE and steel reinforced PE pipes (SRPE) with similar pipe stiffness values for a period of three years. Both were installed under the same conditions, but the deflection results were drastically different. The SRPE had 50% less deflection than the HDPE materials. When re-evaluated for deflection over a period of three years, the HDPE stabilized with high deflection percentages and the SRPE rebounded slightly. The rebound is due to the backfill consolidation around the exterior ribs.
The main point was that the stiffness value did not accurately predict the outcome for all the aforementioned reasons. The steel provides a much more effective pipe stiffness and ultimate strength, which allows for less sensitivity to installation loads and higher allowable covers without applied VAF. Compared to non-reinforced HDPE, the steel reinforcement component of the SRPE provides a much higher modulus, with no creep potential and a much higher wall thrust capacity.
72 pii Must Be Better Than 46 pii Fallacy
The indication of one material type having a larger pipe stiffness would seem logical to indicate it was ultimately stronger, but again using only pipe stiffness for comparison can lead to an apples-to-oranges comparison (i.e., false equivalence fallacy).
A good example is taking fiberglass vs. PVC. Both can be produced at various thicknesses and pipe stiffness minimums. Many believe that since 72 pii is nearly twice as large as the value of 46 pii, then this might be considered twice as strong or can handle twice as much loading. Again, this is grossly inaccurate. Even using the Spangler Modified Formula, which is an over-simplistic way to predict deflection, you can compare directly the percentage of deflection for 72 pii vs. 46 pii pipe types. The difference in deflection is almost negligible if using the same soil stiffness and load conditions. It would seem reasonable that 72 pii material will handle and resist initial deflection, but the value itself will not be the determining parameter for structural performance.
With the example of fiberglass vs. PVC, it could be argued that fiberglass be required to have 72 pii to prevent the initial deflection requirement. Most engineers do not understand per fiberglass specifications the long-term deflection requirement is 5% or less. They confuse this with PVC’s, which has a “long-term” requirement of 7.5% and a short-term requirement of 5%. If using the same rationale for fiberglass, that would make fiberglass’ “initial” deflection control closer to 3%, requiring a much stiffer material performance during handling and installation than PVC if stiffness is so important.
Understanding that pipe stiffness can be affected by the ambient temperature also can show how a low modulus thermoplastic with 72 pii stiffness can underperform compared to a steel reinforced material with a lower stiffness. If temperatures and solar absorption are high, then the lab-tested 72 pii material can actually be as low as 39 pii at the jobsite. The steel material may show little to no change.
There are many engineering factors one should consider when designing for sewer applications. It is easy to become misled by using a simple flattening test that has a misleading resulting value called pipe stiffness. Engineers may want to look closer at other designing properties for structural performance and expectations. Some of those include the modulus of elasticity, tensile strength and results from a stub compression test. These values along with cover charts based on AASHTO design methodology should far outweigh a pipe stiffness value.
Pipe stiffness is first and foremost a check on quality. It does relate to a pipe’s effectiveness in resisting handling and some installation loads, but it is not a determining factor for ultimate load. It should be noted that larger diameter pipes require much lower pipe stiffness for proper installation results as compared to smaller diameters.
Remember, the usage of the test and precedence of 46 pii was born out of the mid-1960s when small diameter PVC collection pipelines grew in popularity across the United States. Much has been learned since other materials have come in favor and much larger sewer pipes are utilized more often for sewerage needs. A pipe generally needs enough stiffness to resist those early loads prior to final installation without deforming excessively. Once installed, the stiffness as defined by ASTM D2412 has little impact to the strength of the pipe carrying soils loads or long-term performance.
Andrew Jenkins and Darrell Sanders, P.E., are with Contech Engineered Solutions: email: [email protected] and [email protected], respectively.
The Professional Development Series is a unique opportunity to earn continuing education credit by reading specially focused, sponsored articles in Informed Infrastructure.
If you read the following article, display your understanding of the stated learning objectives, and follow the simple instructions, you can fulfill a portion of your continuing education requirements at no cost to you. This article also is available online at v1-education.com.
Understand the basics of flexible pipe stiffness
Understand how using pipe stiffness can result in false equivalency performance expectations
Know examples of differences in performance of pipe types with similar pipe stiffness