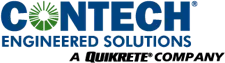
Culverts are unique structures that represent a significant part of today's infrastructure. Many are currently in a state of disrepair or experiencing reduced functionality. Others are outdated from a hydraulic capacity standpoint as changes in surrounding terrain and runoff conditions have resulted in increased flow capacity requirements. Such structures must be inspected on a regular basis to ensure functional hydraulic performance and structural adequacy.
Culverts are too often placed in the same category of jurisdiction and responsibility as bridge structures and, as a result, some of the key issues related to culvert inspection can be overlooked by inspectors who are more familiar with bridge inspection than they are with culvert inspection.
This article will discuss the differences in various culvert materials and how those differences affect a thorough and proper culvert inspection program. Additionally, factors related to culverts in general — including end treatment, slope protection, undermining, clogging, traffic surface treatment and condition, condition of the fill embankment, durability of the culvert material and coating, and realistic service life estimates — will be covered. Also included are key factors and differences associated with the various types of materials used in culvert design and construction . Lastly, the benefits and practical considerations associated with relines, repairs, and rehabilitation of culverts — as opposed to complete removal and replacement — will be discussed.
Culvert inspection involves a combination of skills and experience and requires an intimate knowledge of the types of materials along with an understanding of the design and installation criteria associated with the type of inspected culvert. This article is not intended to be all-inclusive on the subject of culvert inspection but should provide a basic understanding and useful, practical reference information to assist in this process. The FHWA Culvert Inspection Manual is an especially valuable source of information.
Culvert inspection may present hazards to those persons conducting the inspection as well as cause disruptions to traffic flow at the site. Consequently, proper safety precautions are needed to protect workers and the public. Culverts are often located below significant fill embankments and gaining access may expose inspectors to fall hazards. Additionally, attention to confined space risks is required. Culverts should only be inspected during periods of low flow and when conditions are safe to enter. Ideally, inspectors should work in teams. Attention to all applicable state, local, and any other governing agency safety regulations (particularly the provisions of OSHA pertaining to entering confined spaces), combined with common sense, is essential. Inspector training courses and similar indoctrination programs are recommended for culvert inspectors. One should never enter a culvert with questionable structural integrity or under conditions where rapid and sudden increases in flow are likely.
Because inspectors handle both bridge and culvert inspection, it is important to understand some key differences between the two. Unlike bridges, culverts have no distinct separation of substructure and superstructure. Culverts often carry significant amounts of soil overburden loads while bridges generally do not. Many culverts, especially corrugated metal and plastic pipe culverts, function as soil-structure interaction systems, relying heavily on the surrounding soil for support. Even rigid culverts constructed of concrete and stone rely on the surrounding soil to some extent for support and stability. Bridges, on the other hand, tend to be self-supporting — carrying loads from the superstructure to the abutments and substructure.
Culverts function primarily as hydraulic conduits, conveying water from one side of a roadway or similar traffic embankment to the other; therefore, culverts serve the dual purposes of functioning as hydraulic structures as well as acting as traffic load bearing structures. As such, proper inspection must take into account the culvert's hydraulic functionality issues as well as the structural characteristics of the type of culvert material at a given site. Culvert performance is also tied directly to the quality of the surrounding soil envelope and foundation material. Thorough culvert inspection must include attention to these key elements of culvert installation.
Hydraulically, many culverts are designed to function under submerged inlet conditions. As water rises at the upstream end, pressure head increases at the inlet end, forcing added flow through the culvert. Culverts can function properly and efficiently under such flow conditions provided there is attention to proper end treatment and slope stability issues — and the increasing water depth and resultant ponding do not endanger lives or property upstream of the culvert. Most bridges, however, are not intended to function under submerged conditions. Scour at the entrance to culverts and along the length of culvert footings can be a critical aspect of proper culvert functionality. Scour is also a potentially critical concern to bridge foundations and abutments.
Culverts come in a variety of shapes and sizes. Round pipes represent one of the most common culvert types while square or rectangular box culverts are also popular. Arch, elliptical, pipe arch, and modified box culvert shapes are additional shape choices. These various options, combined with the possibility of utilizing single-barrel versus multiple-barrel or multiple-cell installations, essentially covers the gamut of culvert shapes.
Sizes of culverts can vary from approximately 12- to 144-inch diameters for round pipe choices, to larger than 50-foot-span culverts when dealing with field-bolted structural plate or large precast concrete culverts.
The shape and number of barrels selected for a specific culvert crossing are site-specific determinations. Culvert selections are typically made with the intent to convey as much water in as little vertical headroom space possible while conforming to the stream cross section and right-of-way constraints. Often, the primary considerations affecting culvert selection are directly related to local regulations governing stream encroachment, stream alignment, wetland stipulation, and fish passage. Regulations may prohibit changes to the type of invert or stream bed, requiring clear span arches or three-sided boxes rather than full barrel culverts.
Culverts are supplied in a variety of materials, including corrugated metal, plastic (solid wall and profile wall pipe), concrete (reinforced and unreinforced), and stone. Each material type has specific design criteria and installation techniques that apply, as well as a unique set of guidelines to follow and factors to consider in relation to culvert inspection. Culvert inspectors must be familiar with the necessary criteria for each material type to conduct an accurate and meaningful inspection.
All culverts should be inspected for clogging, material build-up in the invert or on the interior walls, and other flow restriction issues. Thorough inspection also includes attention to end protection, slope stability, undermining, joint integrity, and any changes to traffic surface conditions.
Additionally, corrugated metal and structural plate culverts need to be inspected for any shape changes, significant deflections, cracking at bolted seams, and significant loss of coating or metal. Plastic pipe culverts should be checked for shape changes, significant deflections, stress cracking, and inner wall buckling. Concrete pipe culverts need to be checked for significant wall cracking, concrete spalling, differential settlement between pipe sections, and joint separation. Stone culverts need to be inspected for deterioration in the stone structure, spalling of the culvert walls, and shape changes.
Single inspections, while valuable, are a "point-in-time" snapshot of the culvert's condition. Proper culvert inspection must also consider the history of the culvert in question. All culverts should be assessed as to their potential for risk and a regular inspection schedule should be established. It is suggested that culverts be inspected at least every five years, following periods of high flow and extreme storm events, and/or whenever significant changes — such as new development resulting in increased runoff or channel alterations — occur upstream of the culvert. Follow-up and more frequent inspections may be required depending on the type and extent of any problems found during the inspection process. Such data will prove invaluable in assessing the amount and rate of any changes that may be occurring. This history will also serve as a guide in deciding what remedial actions may be required.
Logical and organized culvert inspection forms combined with a regular inspection schedule and good record-keeping processes are essential in maintaining an inventory of stable, functional culverts. Sample culvert inspection forms are included in several of the references listed on page 6; specifically the AREMA Manual (Fig. 1-4-28) and the FHWA Culvert Inspection Manual (see Chapter 4). These forms can be used as guides and can be modified as required to fit specific needs.
The culvert inspection process starts with the collection of accurate baseline measurements that will serve as benchmarks for future culvert inspections. Typical baseline measurements include the following:
Frequency of inspection will be dictated to some extent by the condition of the culvert and the significance of any deficiencies discovered in the inspection process. The intent is to detect changes and determine if condition is stabilized or worsening. Follow-up inspections will discern this.
Items to evaluate, assess, and note during a culvert inspection include the following:
Corrosion may be occurring due to chemical content of the soil, effluent, or both. Such corrosion is typically evident by rusting, metal loss, and/or perforations in a metal culvert. Spalling of concrete and exposed or rusting reinforcing steel is typically seen in concrete culverts subject to corrosive attack. Note the extent of such damage and assess any significant loss of strength and stability in light of the applied loads. Additionally, identify the source of such corrosion.
Abrasion is evident when the surface of the culvert — primarily the invert — is worn away by the flow forces and the bed load carried by the flow through the culvert. Culverts installed on fairly steep gradients, combined with sites that have a high concentration of potentially abrasive bed loads such as sand, gravel, and rock, are candidates for damage from abrasive forces.
Coating loss should be noted as this can lead to further damage and deterioration of the culvert wall section. Identify the source of such coating loss.
Perforations are typically associated with metal culverts. These can be minor and of little consequence in many instances. In fact, corrugated metal pipe is frequently supplied with perforations in subdrainage and recharge pipe applications, but the culvert should still be evaluated for the extent of metal loss to determine if this will have a significant effect on the structural strength of the culvert wall and if there would be any appreciable loss of backfill due to the presence of such perforations.
Cracks are typically seen in concrete culverts, although metal and plastic pipe culverts can also exhibit cracks on occasion. Note the extent of such cracking including the size, length, location, and frequency. The cause of such cracking needs to be identified and corrective action taken. Cracks in metal culverts can possibly be repaired by welding bar stock material compatible with the host pipe wall across the cracks. Such repaired areas should then be coated or painted with a suitable inert coating material for protection. Concrete cracks may be repaired by spot patching.
Joints should be investigated for proper alignment, fit, and tightness. Misaligned, ill-fitting joints need to be addressed, evidence of backfill loss noted, and appreciable loss of fill remedied.
Seams should be properly aligned with the plates meshed and indexed where applicable. Poorly constructed and misaligned seams can lead to a loss of fill and reduction in culvert strength.
Shape changes and deflection should be noted as to location, length of culvert section involved, and severity. A logical measurement scheme to determine the shape change is a valuable tool to assess a culvert's condition. See Figure 1 for a method to determine the actual radius of curvature of a culvert wall section for comparison with design radius.
Undermining of the ends or any interior sections of the culvert should be noted and addressed. Condition of the slopes and any end treatment or protection should be noted. Such items as endwalls, cut-off walls, headwalls, and slope collars should be checked for alignment, deterioration, and cracking. Slope failures and evidence of significant fill scouring also need to be noted and appropriate corrective measures taken.
Culverts are an essential yet unique feature of our infrastructure. As such, proper design and installation, routine inspections, and appropriate remedial actions to ensure continued functionality and stability are required. Understanding the differences in the various culvert materials and the associated problems is critical to this process, thus proper and thorough culvert inspection is often best left to experts. Establishing procedures where culvert inspections are conducted in a timely manner with logical and accurate data combined with an appropriate follow-up action plan are all fundamental aspects of sound culvert infrastructure management.
Jim Noll, P.E., is the director of Engineering Services for CONTECH. He has 34 years of experience in the corrugated metal pipe industry and is an active member of various technical organizations, including ASCE, AREMA, NCSPA, and ASTM.
Robert (Bob) Frascella, P.E., is a civil engineer with the Burns Group and has more than 35 years of professional experience. He currently specializes in consulting engineering for large rail transit projects under development in the United States. He is an active member of AREMA where he serves as chairman of the sub-committee on culverts.
Online quiz for this article is not active and
PDH credit is no longer available.
This article is being maintained for informational purposes only.
How to recognize the key differences between culverts and bridges from an inspection standpoint.
The critical aspects of culvert inspection including proper training and attention to safety-related issues.
The frequency of culvert inspection and the need for accelerated inspection schedules in some circumstances.
The options for addressing culvert deficiencies including repair, reline, rehabilitation, and replacement.