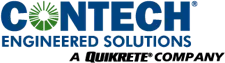
Manufactured Treatment Devices (MTDs) are similar to non-proprietary stormwater BMPs in that they must be maintained so they perform as intended. However, the majority of effort and focus is placed upon the initial design and construction of stormwater treatment facilities, with little thought as to how these systems will be maintained long-term. The property owner, in all cases, is left responsible for the consequences of decisions made by others during the design and construction phases, nearly all of whom have moved on to new projects after the construction phase of the project is terminated.
This is changing, as civil engineers are now placing more importance on the long-term maintenance costs associated with MTDs. To serve the best interest of their clients, not only does the specifying engineer have the responsibility to select and design the stormwater BMP that meets the site’s structural and regulatory requirements, they also have a responsibility to consider long-term cost of ownership as well as initial capital costs.
Before we explore how to select and design MTDs to reduce long-term maintenance costs, we need to explore what drives these costs. The four primary cost influencers are 1) time and equipment, 2) disposal costs, 3) replacement costs of consumable components, and 4) frequency.
Time and Equipment
Time and equipment costs include the labor and equipment needed to perform maintenance. Distance to the disposal facility is also a factor. The more people, time and equipment required, the higher the maintenance costs.
Disposal Costs
Municipalities may have their own maintenance crews and access to disposal facilities. Privately owned facilities such as retail establishments or apartment complexes will usually hire a third-party maintenance provider. These providers will need to pay to have their contaminated liquids and solids disposed of properly. Local regulations dictate how these materials are managed. However, solids typically go to a landfill, while liquids usually go to a water treatment facility. The maintenance providers must pay for the disposal of these materials.
Consumables
The type and amount of replacement consumables such as filters, media and mulch will also impact total maintenance costs.
Frequency
How often does the manufacturer recommend the MTD be maintained? Is there operational history for the MTD available in similar applications that demonstrates that it can continue to perform as designed while being serviced at the recommended interval? The frequency of maintenance events will have the most significant impact on the total cost of ownership for an MTD.
When selecting an MTD, selection criteria usually fall into three buckets: performance capabilities, cost and ancillary benefits.
On the performance side, we are usually asking if the permitting authority will approve the MTD we are considering, will it work with local site constraints, and will it meet project pollution removal goals? On the cost side, there are both the capital cost (purchase price) and the long-term operation and maintenance costs. The third bucket contains things that don’t fit into the first two buckets, such as ease of design, ease of installation and the like.
The first question is the most important: Is the MTD approved? The two premier MTD verification and certification programs in the United States are the State of Washington Department of Ecology Emerging Stormwater Treatment Technologies (TAPE) and the New Jersey Department of Environmental Protection Certification Program. These programs are relied on by more than 30 different agencies outside of New Jersey and Washington. These programs require peer review of laboratory and field testing following standardized testing protocols to determine the removal efficiency of different MTDs at different operating rates.
These programs do an excellent job of providing data that allows comparison of the performance of one MTD to another and comparison of the performance of a particular MTD to an established performance standard. However, they do not require that in-field maintenance intervals be demonstrated to meet maintenance interval claims during testing. As a result, some systems have sacrificed longevity for increased design hydraulic loading rates, which generally result in smaller, lower capital cost systems. This, combined with the fact that there is often poor communication among the people who are responsible for the long-term maintenance of systems and those who are designing and approving them, means that long-term maintenance costs are often ignored in the BMP selection process. As a result, some MTDs have vastly different default maintenance recommendations as compared to the actual maintenance histories observed during field testing.
For example, Figure 1 shows the estimated annual maintenance costs of biofilters with General Use Designation (GULD) for Basic Treatment under the TAPE program. To gain GULD approval, the biofilters must achieve at least 80% TSS removal when influent concentrations are above 100 mg/L and no greater than 20 mg/L effluent concentrations when influent concentrations are between 20 and 100 mg/L. Biofilter A only required two maintenance events during the testing process, while biofilters B and C required six and nine, respectively. When the maintenance cycles observed during the testing period that led to regulatory approval differ from those in the manufacturer’s marketing material, this creates a risk that the actual annual maintenance costs may be much higher for that MTD. Or, if the MTD is maintained at the recommended interval but actually needs much more frequent maintenance to continue to perform as designed, too much runoff will bypass treatment, and water quality will suffer. This is something every engineer should consider when specifying an MTD.
The three factors that are most important to consider when designing MTDs with maintenance in mind include access, location and onsite logistics.
Access
When talking about access to the MTD, the first thing we think of is manhole covers, which are the most common choice as they are inexpensive (typically under $1,000) and easy to work with from an inspection and maintenance perspective. The most commonly used manhole cover sizes are 24” and 30”, and they are rated for heavy-duty traffic loading. Other options can provide more access to the internals of certain devices, but there is often a tradeoff between accessibility and cost.
Trench covers allow access to the entire top of the structure, but they’re more expensive (typically over $1,000), can be difficult to remove, and are not the most aesthetic option. They are available in 24” width x various lengths to accommodate different MTD vault sizes, and they are typically rated for heavy-duty traffic loading. Hatches (Figure 2) also offer excellent access, are hinged for easy opening, but are the most expensive option (typically over $2,500). A 48” x 48” hatch is frequently used on MTDs. Hatches come in many different square and rectangular options as well as different load ratings, including pedestrian, non-heavy duty traffic and heavy-duty traffic.
At times, a combination of covers can be used, with traditional manhole covers being used for inspection ports and a hatch located where confined-space entry is needed. Most access castings can be sourced in a heavier duty load rating when required for projects such as airports or shipping terminals.
Location
Another critical factor is the physical location of the device on the site. Manhole covers, trench covers and hatches are not visually appealing, and they may present a trip hazard. As such, placement in walkways and in front of entrances should be avoided.
Attention should also be given to the frequency of inspection and maintenance events as well as how they impact both pedestrian and vehicular traffic at the site. Inspection events will typically last 30 minutes, while maintenance events may take 30 minutes to several hours to complete, depending on the type and size of the MTD. These events will usually take place during regular business hours. The engineer needs to assess both vehicular and pedestrian traffic flows to see how these events will impact movement.
Onsite Logistics
Closely related to location is onsite logistics. Different MTDs require various maintenance activities. An engineered bioretention system may be possible to maintain with minimal crews and equipment. In contrast, most underground systems will require a vacuum truck, support vehicles and possibly space for the staging of consumables.
Special consideration needs to be given to those systems that will utilize a vacuum truck for maintenance. Vacuum trucks can weigh up to 25,000 lbs and should not be driven on grass or landscaped areas. Also, vacuum trucks usually charge per hour of service. Generally speaking, there is a tradeoff between a vacuum truck’s efficiency and capability. The closer the MTD is to the truck, and the shallower the system, the more efficient the vacuum truck can be, and less time will be needed for the maintenance event. The deeper the system—or the farther away it is from the vacuum truck—the less efficient the vacuum truck will be, and the longer the maintenance event.
Hydrodynamic Separators
Hydrodynamic separators (HDSs), also known as oil/grit separators (OGSs), are widely deployed as stormwater treatment BMPs, both in standalone applications and as pretreatment devices in a treatment train. The primary treatment mechanisms used in HDS units are gravity separation and spill capture. High-specific-gravity particulates settle by gravity to the sump of the device, and low-specific-gravity oil, trash and debris float to the surface and are trapped.
The inspection of HDS systems is usually performed twice a year at grade, without the need for confined-space entry. Inspections should quantify the accumulation of hydrocarbons, trash and sediment in the system. Measuring pollutant accumulation can be done with a calibrated dipstick, tape measure or other measuring instruments. When the sediment level reaches a predefined point, as indicated by the MTD manufacturer (such as a percentage of the sump area), maintenance is recommended. The use of a vacuum truck is generally the most effective and convenient method of removing pollutants from HDS systems. The system should be completely drained, and the sump fully evacuated of sediment and any internal components sprayed down to remove any build-up of pollutants.
Since not all HDS systems are maintained the same way, engineers should inquire as to the following to ensure long-term maintenance costs are reduced:
Is confined-space entry required?
How many access points are needed?
Is disassembly of internal components needed?
Media-Based Filter Systems
Many manufactured stormwater filter systems use media-filled cartridges. During a storm, runoff passes through the filtration media, which absorbs and retains pollutants from stormwater runoff, including total suspended solids, hydrocarbons, nutrients, metals and other common pollutants. The structures that house the filter cartridges can be constructed in a variety of ways to accommodate a wide range of flows, project footprints and variable hydraulic conditions. Standard configurations include catch basin, manhole, vault, curb inlet and linear grate.
The inspection of media-based filter systems is usually recommended once per year and additionally after major storm events. Inspection procedures differ by the manufacturer, but in most cases, visual indicators are used to evaluate the need for maintenance. Factors such as the amount of accumulated sediment, sediment loading on top of the cartridge, submerged cartridges, a pronounced scum line or plugged media may all be indicators of the need for maintenance.
Media-based filter systems require the most intensive maintenance of any MTD. Maintenance of media-based filter systems includes the removal of accumulated sediment, spraying down the interior and replacement of media cartridges. Depending on the size and location of the unit, maintenance can take several hours to complete. Maintenance personnel will be required to enter the vault to perform the maintenance, and a vacuum truck will be needed to remove sediment.
The process for removing the spent media cartridges differs considerably by manufacturer, and these differences can have a significant impact on the time needed for cartridge replacement. When evaluating media-based filter systems, engineers should inquire as to the following to ensure long-term maintenance costs are reduced:
Do the cartridges have a hood or skirt to prevent debris and oil from clogging the media surface? Do the cartridges have a surface-cleaning mechanism?
How long is the targeted media replacement maintenance interval? Is there operational data available to support the recommended maintenance interval?
Does the manufacturer offer a cartridge exchange program?
How much do replacement cartridges cost?
Are tools needed to remove the media cartridges? How fast can the cartridges be removed?
Bioretention Systems
Engineered bioretention systems, sometimes referred to as tree box filters, target the removal of suspended solids, total and dissolved nutrients and metals, oil and grease, trash, and debris. Components typically include plants, mulch and specially designed filter media mixtures often contained in a concrete container. The mulch layer and filter media capture and immobilize pollutants during storm events. Between storms, those pollutants decompose, volatilize, and are incorporated into the biomass of the system’s micro/macro fauna and flora. Stormwater runoff flows through the media and into an underdrain system at the bottom of the container, where the treated water is discharged. The high media flow rate reduces the footprint of these systems compared to traditional bioretention.
Inspection and maintenance of bioretention systems may take less than 30 minutes and is the least expensive to maintain of any stormwater MTD. Maintenance typically does not require a vacuum truck or confined-space entry and is typically recommended twice per year. Additional maintenance may be necessary depending on sediment and trash loading. Maintenance activities may include inspection of the vault and surrounding area; removal of tree grate and erosion control stones; removal of debris, trash and mulch; mulch replacement; and plant health evaluation and pruning or replacement as necessary.
The design of engineered bioretention systems differs considerably by manufacturer, with some including components such as screening devices, filter cartridges and sediment chambers. These differences can have a significant impact on the cost of maintenance. When evaluating engineered bioretention systems, engineers should inquire as to the following to ensure long-term maintenance costs are reduced:
Is the first year of maintenance included?
How long is the recommended maintenance interval?
Does the system utilize a pretreatment chamber with filters?
Does the system utilize filter cartridges?
Every MTD needs to be maintained, but the frequency and costs associated with MTDs differs substantially by manufacturer. In some cases, recommended maintenance intervals are significantly longer than the maintenance intervals that were required to demonstrate adequate performance in field trials. Engineers who wish to lower the long-term maintenance cost of MTDs for site owners need to examine the maintenance guidelines of various devices and ask maintenance-related questions during the evaluation process to ensure the system they specify will indeed provide the lowest total cost of ownership.
Brynn Laird, P.E., manages Contech’s Stormwater Engineering department for the eastern U.S. and Canada. Brynn has 10 years’ experience in the stormwater industry and holds a Bachelor of Science degree in Civil Engineering from Virginia Tech; email: [email protected].
Travis Wolfe is Contech’s Maintenance & Field Operations Manager for the western U.S. Travis has 14 years’ experience in the stormwater industry. Drawing from his field experience with private and municipal maintenance crews, Travis promotes a practical approach to the maintenance and operation of stormwater treatment systems; email: [email protected].
Vaikko Allen, CPSWQ, LEED-AP, is the Director of Stormwater Regulatory Management for Contech Engineered Solutions, where he assists regulators, engineers and environmental organizations in the development and implementation of stormwater regulation; email: [email protected].
Online quiz for this article is not active and
PDH credit is no longer available.
This article is being maintained for informational purposes only.