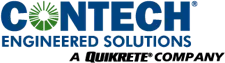
The application of a hard armor system such as articulating concrete blocks as an erosion control mechanism demands diverse performance characteristics, only some of which are accomplished by the armoring itself. For this reason, all such systems involve more than one layer. In some specialized circumstances, as many as five layers above the subgrade may be necessary. Proper analysis of the site conditions, assessing the expected hydraulic and hydrologic conditions, determining the desired design life of the system, and outlining the intended level of protection are all crucial to a successful installation. Choosing the right subgrade protection is just as important as selecting the right armor layer.
Two typical armor system sections are shown in Figure 1. The simplest hard armor system involves a geotextile layer directly on top of the subgrade, held in place by an articulating concrete block layer. This is used for situations where the erosive threat is flowing water and little, if any, other surface loading is expected. For example, this type of system is applied in a landfill down-drain chute.
More complex erosive conditions demand differing protection measures. In cases where the armor layer will be subjected to vehicular loading in addition to the hydraulic conditions, additional layers may be necessary to better distribute the wheel loads, allow for improved drainage, and contain/ separate the drainage layer from the other layers. These layers take the form of geotextiles, geogrids, and rock. These types of applications include boat ramps and lowwater crossings.
In general terms, geotextile layers are the most versatile and widely applied protective system. Geotextiles may be woven — with fibers in two well-defined directions roughly perpendicular to each other — or non-woven and resembling felt, in which the fibers are not generally aligned in any particular direction. Although it's rare, some geotextiles are knit. In all cases, the fibers are synthetic so that they will not biodegrade (when protected from UV exposure), and can be expected to remain functional for the project lifetime. In the context of hard armor applications and especially with articulating concrete block mats, geotextiles serve the functions of separation, filtration, and drainage. In many installations, the geotextile is in direct contact with both the subgrade and the armorlayer above.
Geotextiles are broadly defined by their physical, mechanical, and hydraulic properties. In hard armor applications, two of the hydraulic properties are the most critical to consider: Apparent Opening Size (AOS) and Permeability. Durability is a mechanical property and, depending on the application, must also be evaluated. The AOS is defined as the U.S. Standard Sieve number that has openings closest in size to the openings in the fabric, and is reported in those terms — or in millimeters. It represents the smallest size particle that will not pass through the geotextile. This property will be compared with the average diameter of the subgrade soil (d50) in the design process. The permeability of the geotextile (sometimes called the crossplane permeability) is a measure of the capacity for water to flow through the material, and is generally reported either directly (as permeability, in units of cm/second or inches/second), or as a function of the thickness of the material (as permittivity, in units of sec-1), which would then be multiplied by the thickness of the selected layer to determine the permeability. This is a quantification of the ability of the fabric layer to act as a filter, or to minimize differences in hydrostatic pressure (for example, in installations under wave attack). In the design process, this property also will be compared with the permeability of both the subgrade and, in more complex sections, the overlying layer. The permeability requirement is such that the geotextile must be at least 10 times more permeable than the subgrade soil:
Kg > 10Ks
where:
Kg = Permeability of geotextile (cm/second)
Ks = Permeability of subgrade soil (cm/second)
The geotextile also must retain the coarser particles of the subgrade while remaining permeable enough to allow infiltration and exfiltration to occur freely. It is not necessary to retain all the particle sizes in the subgrade. In fact, it is sometimes beneficial to allow the smaller particles to pass through the geotextile, leaving a coarser substrate behind. Either woven or non-woven needlepunched fabrics may be specified. If a non-woven fabric is used, it must have a mass density greater than 12 ounces per square yard (400 grams per square meter) when used as part of a hard armor system. Note: Under no circumstances may a spun-bond or slit-film fabric be allowed under an articulating concrete block armor system.
In most riverine applications with a non-cohesive bed material, the particle retention requirement dictates that the AOS — also known as the O95 — of the geotextile must be less than the effective diameter of the 90th percentile soil particle (d90) of the subgrade soil. For example, the particle larger than just 10 percent of all other component soil particles. However, in areas of high turbulence, the AOS should be less than the mean particle size (d50) of the soil. It is not uncommon to use one type of geotextile on the bank soils, and a different type on the bed. Figure 2 provides a flowchart developed under NCHRP Project 24-23 to assist in the selection of a geotextile filter for use with articulating concrete block systems.
Separate from the hydraulic aspects of the geosynthetics, the mechanical property of durability must be evaluated, especially during the time after installation but before construction is complete. Geosynthetics are most susceptible to damage during this time because they are exposed. During the design and specifying process, the designer should ask, "What degree of survivability during construction will the geotextile need in order to function as designed?" AASHTO M288 Geotextile Strength Property Requirements is the most current method used to address the strength needed by the geotextile to accommodate the construction environment. Specifically, there are three classes defined to address these construction tolerances, including:
Some armor sections also require a geogrid. Geogrids serve different functions depending on the section in which they are used. In cases where vehicular traffic is anticipated and the subgrade soils are relatively poor, the geogrid can help distribute the applied loads to prevent rutting and to reinforce the driving surface. The tensile strength of the grid is important to consider in these cases. Selection of the proper strength geogrid with regard to subgrade improvement under expected vehicular loading should begin with ascertaining the soil characteristics.
Geogrids can also be used to contain larger diameter layers directly below the armoring layer when there is a larger percentage of open area, potentially allowing the gravel to escape. In these instances, the aperture size must be considered — a property similar to the AOS of a geotextile.
In instances where either the geotextile or geogrid is in direct contact with the overlaying armor layer, it is advisable that the geosynthetic layer not be attached to the armor block. Doing so can lead to damage in the geosynthetic layer that can defeat its purpose.
In the design of any armored erosion control system, the first step is to identify the properties of the subgrade that need to be protected. This typically entails at least a surficial geotechnical investigation to obtain a soil gradation profile and the permeability of the soils. In instances where it may be encountered, the subsurface elevation and characteristics of the groundwater table should also be ascertained. Because an armored system is being designed, the expected surface flow characteristics will typically have been determined. However, if they have not, then the velocity and shear quantities should be determined at this point in order to size the top armor layer properly.
Once the characteristics of the subgrade soils are known, the geotextile layer to protect it can be specified. To protect the subgrade soils adequately, the geotextile layer should be selected to have an AOS equal to or less than the d90 (or, as the case may be, the d50) of the subgrade, and permeability at least 10 times greater than that of the subgrade. This will ensure any hydrostatic pore pressure is relieved even if the armor layer blocks much of the surface of the geotextile, while still retaining the subgrade soils in place. This is particularly important in areas under wave attack, when the maximum hydrostatic pore pressure could potentially coincide with the lowest water level (maximum rundown).
In a similar fashion, geogrids can be selected by choosing an aperture size smaller than the average size of a drainage layer beneath it. The strength should be enough to adequately distribute the vehicular loads as well, with the intent of providing an increased modulus — hence a lateral confinement to the system. The intent is to limit the tendency for the lower layer to spread out beneath repeated traffic loads.
The last step is to specify the desired system. While this step seems straightforward and simple, the large variety of available geotextiles in the marketplace makes this portion of the task more challenging and can introduce confusion. Manufacturers offer many different types of woven and non-woven alternatives that would qualify for the application. Specifying the "correct" one is often more of a description of the desired performance — or a Performance Specification — than it is the identification of a specific one. This can be accomplished by identifying the elements outlined above. It is up to the designer to determine the appropriate strength and hydraulic properties of the geosynthetic for the site soils and anticipated construction conditions, and then ensure any offered alternatives meet the intent of the Performance Specification.
Preparation of the subgrade is a vital component of a successful hard armor erosion control system. The specifier can take steps to ensure that the preparation will be performed adequately for system installation. In particular the specification should include language that requires the slope to be graded to a plane smooth enough to ensure intimate contact between the slope face and the geotextile/filter fabric, and between the geotextile and the overlying armor layer. Any deformities in the slope, roots, stones, and/ or grade stakes projecting normal to the local slope face should be regraded or removed. Holes, footprints, grooves, depressions, or other voids or protrusions greater than 0.5 inch normal to the local slope face shall be regraded and eliminated. Compaction, depth of fill layers, and homogeneity of the soils should be identified in the specification as well, consistent with good engineering practice and applicable local requirements.
In many applications, it is prudent to require an inspection of the subgrade preparation by, at a minimum, the specifying engineer and/or the owner's representative before geotextile or armoring system placement. These inspectors must express approval before any of the components of the armoring system can be installed. The geotextile placement should be specified as "free of folds or wrinkles" and overlap upstream to downstream in a shingle fashion. Longitudinal and transverse joints should be overlapped by at least 2 feet.
Where required, a drainage layer of angular crushed rock, containing no fines, can be specified. The size will depend on the application, but should also be consistent with the permeability ratio of 10:1 detailed above.
Proper specification and installation of the geosynthetic layers will provide a long service life for the hard armor erosion control system, at an economical initial price.
Matthew Stovall, P.E., LEED AP, is an inside project consultant for CONTECH Construction Products Inc., and provides technical support for bridge, hard armor erosion control, and specialty products in the Western United States. He is a graduate of the Georgia Institute of Technology in civil engineering and also holds a Certificate in Coastal Engineering from Old Dominion University.
Barrie King, E.I.T., is the supervisor of engineering for Contech Construction Product's Armortec product line.
Online quiz for this article is not active and
PDH credit is no longer available.
This article is being maintained for informational purposes only.